
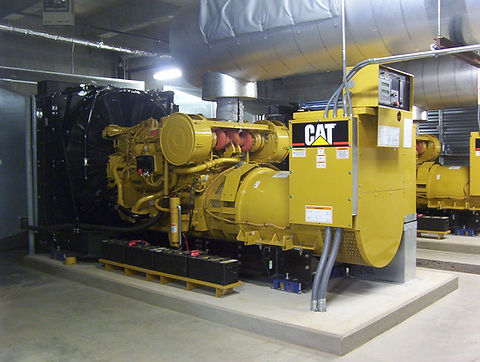
FEATURED PROJECTS
We are specialized in the consulting engineering services including healthcare, broadcast, manufacturing, mission critical, and other high end technologies sectors.

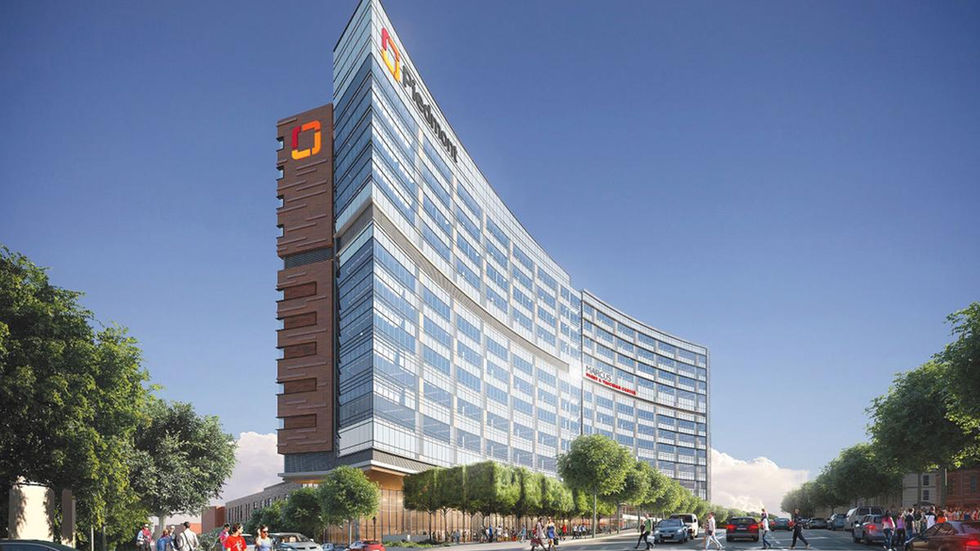




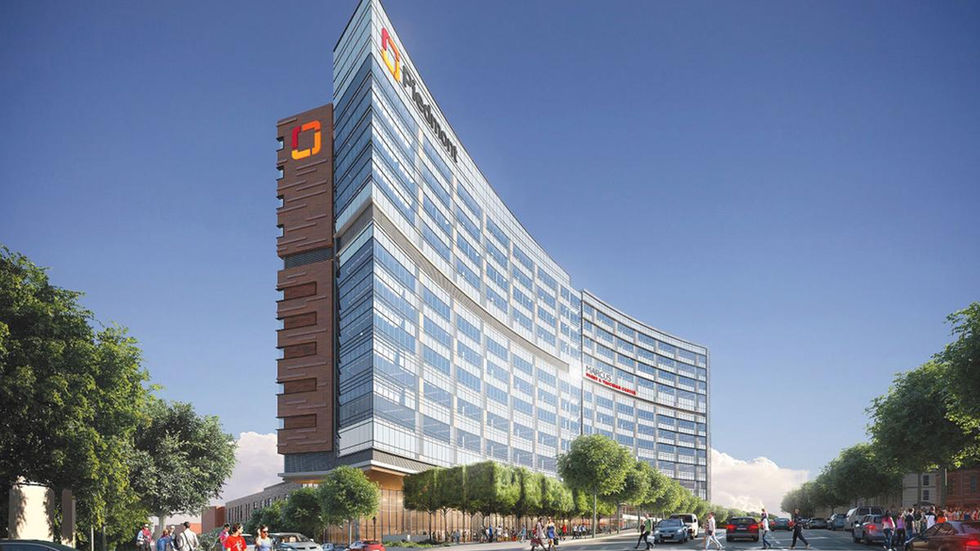




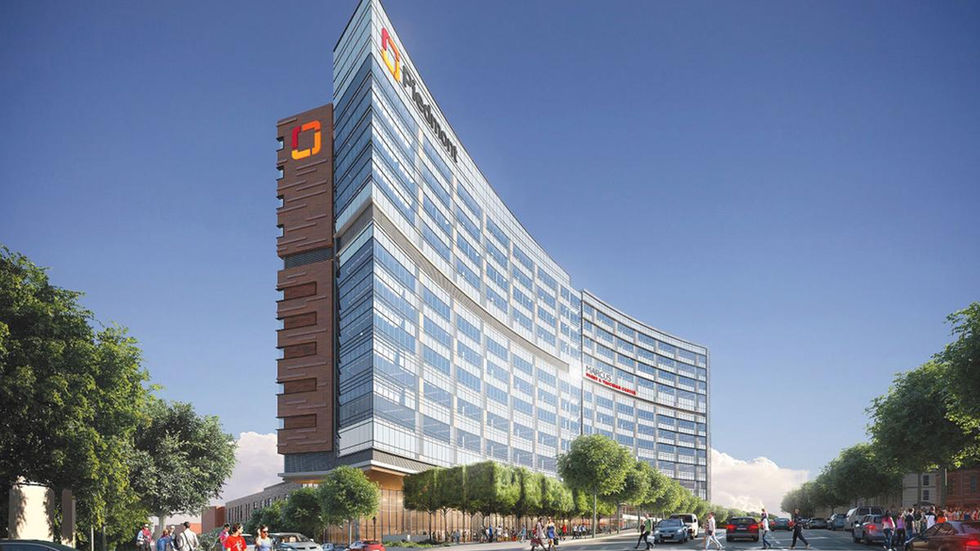




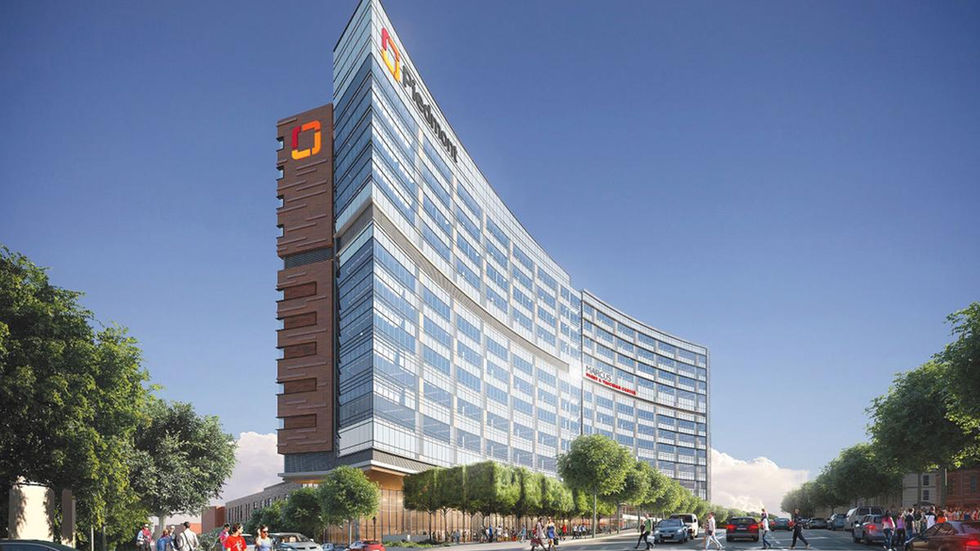




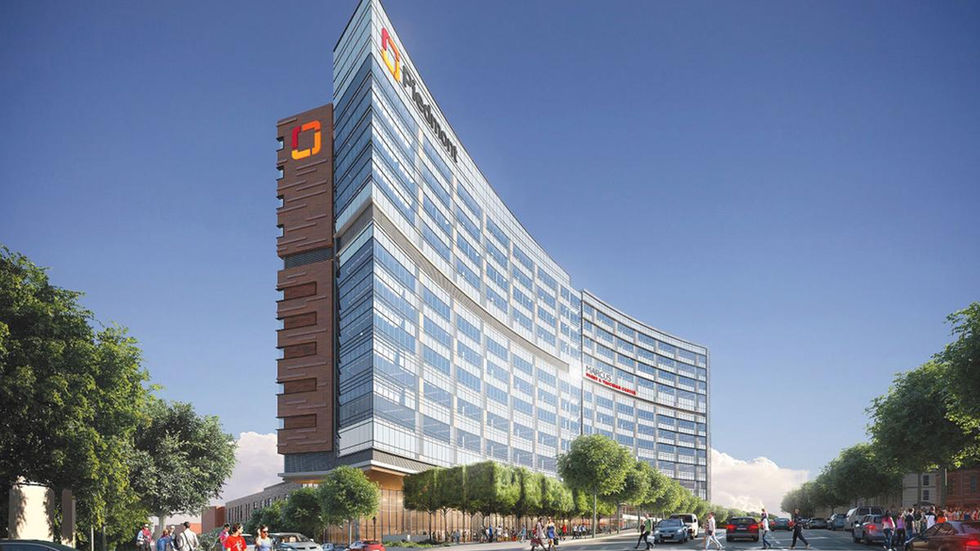




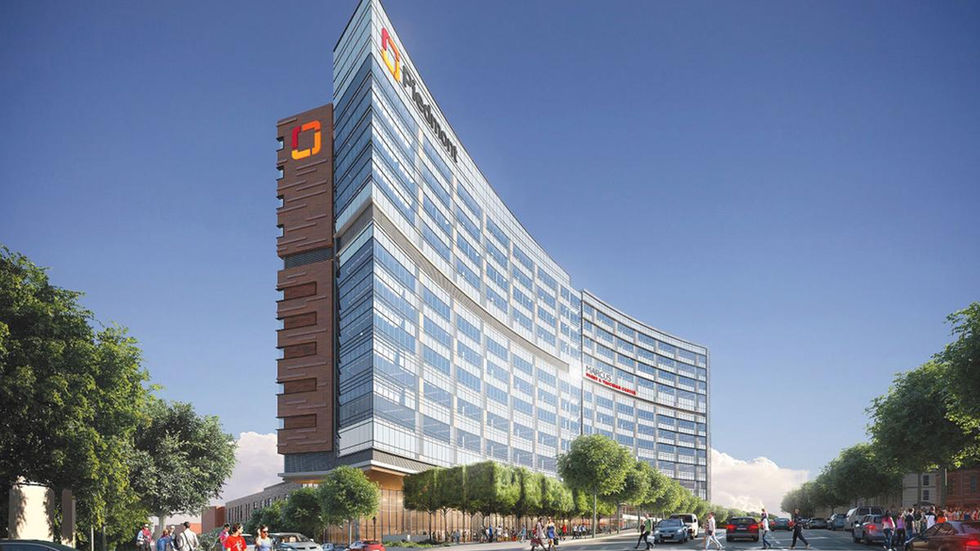



EQUIPMENT REPLACEMENT
AND INFRASTRUCTURE PROJECTS
SOUTH GEORGIA MEDICAL CENTER - VALDOSTA, GA
POWER PLANT

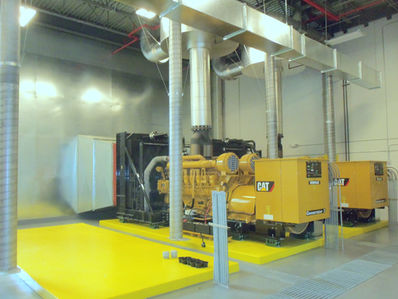
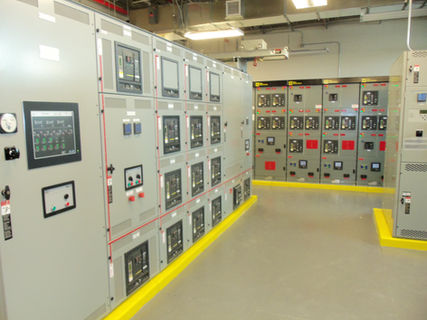

SOUTH GEORGIA MEDICAL CENTER - VALDOSTA, GA
POWER PLANT
Central Energy Plant Upgrade
HPD was Contracted as the Prime Consultant for the project. Faced with an aging and inadequate Chilled Water system, SGMC engaged HPD to design a replacement system. HPD surveyed the existing system and met with owner representation to determine current and future requirements. HPD worked as a team with SGMC administration to discuss the owner's operational requirements and the effects on the power system. The new design increased the capacity of the existing chiller plant by building a new cooling tower/pump yard, increasing the piping headers and replacing the existing chillers with larger 1200 - ton chillers.
New Generator Plant
HPD was contracted as the Prime design Consultant to construct a 5,500 sq.ft. facility to house new normal and emergency services. Armed with the functional requirements, which included feeding a chiller on emergency power, HPD evaluated and presented numerous options to meet the owner's requirements. These options evaluated multiple generator configurations, equipment locations replacing equipment in place, and budget constraints. Ultimately, the evidence pointed towards constructing a new free- standing building to house new normal and emergency service equipment. The normal plant consisted of 4-2500 kVA service transformers that feed two Main-Tie-Main switchgear lineups. The Emergency plant consisted of two parallel 1750 kW generators with provisions for a third generator. The facility utilizes energy efficient lighting and controls and included a power monitoring systems to monitor, measure, and record the energy use. The proximity of the building required numerous utility relocations and modifications including sewer, Oxygen Farms, Med Gas, fuel-oil, and electrical. Virtually every utility for the hospital was impacted. The project was constructed in phases to allow the hospital to remain in operation during these utility relocations. In addition, SGMC was also constructing a bed tower and parking deck which adjoined the project site and would be fed from the new power plant. HPD worked with the other design and construction teams to seamlessly integrate their power requirements and schedules into our project. The final phase of the project was to back feed the existing facility. The entire facility would experience a shutdown for this migration. HPD worked with the owner and contractor to determine a phasing solution to migrate the existing electrical systems on to the new facility and to decommission the old emergency and normal power plants. The end result was a modern, energy efficient power plant that will continue to serve SGMC into the future.
SOUTH GEORGIA MEDICAL CENTER - VALDOSTA, GA
OPERATING SUITE HVAC UPGRADE


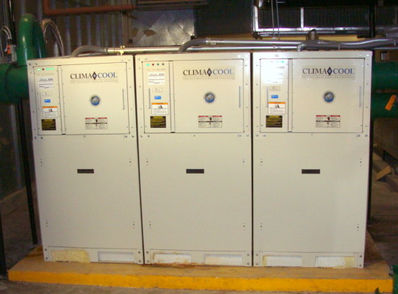

SOUTH GEORGIA MEDICAL CENTER - VALDOSTA, GA
OPERATING SUITE HVAC UPGRADE
Surgery Suite Sub Cooling HVAC Upgrade (ASHE Award Winner)
SGMC contacted HPD, LLC regarding complaints from their surgery staff in the Operating Rooms.
HPD provided the mechanical, electrical, plumbing (MEP) consulting engineering services for several projects on the Campus including two Open Heart Operating Rooms with dedicated HVAC systems including glycol sub - cooling. Review of the existing conditions revealed that the new O.R.’s were maintaining satisfactory conditions. However, the remaining eight O.R’s and two Cysto Rooms were experiencing high humidity at lower temperature conditions.
The existing systems that served the eight OR areas were installed in 1984 and consisted of two - chilled/water hot water air-handling units with direct expansion, sub-cooling coils. The VAV’s had been replaced previously and incorporated direct digital controls capabilities.
Smoke removal was accomplished through a smoke relief cycle in the air handling units.
HPD and SGMC developed an upgrade plan for the HVAC system to accommodate the requirements while minimizing down time and introducing new technologies as follows:
-
The air handling units would be changed out one at a time so half of the OR Suite could remain in operation. The new units would be Fan Wall Systems for the supply and return fans.
-
New dedicated chilled water pumps would provide chilled water to the main chilled water coils.
-
Modular Chillers would be utilized to provide 32 degrees glycol to the sub-cooling coils in order to meet the required designed space conditions.
-
A new dedicated steam to hot water heat exchanger system would provide 200 degree space heating hot water to allow the room temperature to be raised to set point within 15 minutes.
-
The entire control system would be upgraded to DDC. Room temperature and humidity control and display would be accomplished by touch screen technology room monitors.
-
Smoke exhaust would be provided by a dedicated exhaust fan for every two rooms.
The Mechanical contractor served as the Prime Contractor and coordinated the construction phasing and process to reduce down time and maintain environmental conditions in the OR’s that remained operational.
The end result provided new air handling systems with HEPA filtration, new humidification, sub-cooling and touch screen room control that allowed the staff to change temperatures from 72 degrees down to the designed 62 degrees in 15 minutes while maintaining below 40% relative humidity. The staff could also raise the temperature from 62 to 70 degrees after the case was completed.
A reset unoccupied mode allowed the glycol system to be deactivated and the chilled water system reset to maintain room conditions of 78 degrees and 50% relative humidity.
TIFT REGIONAL MEDICAL CENTER – TIFTON, GA




TIFT REGIONAL MEDICAL CENTER – TIFTON, GA
Central Plant Upgrade / Energy Study
Challenged to find methods to reduce energy cost, plan for future projects and streamline operations Tift Regional Medical Center (TRMC) engaged HPD to team with them to identify, analyze and substantiate a plan to meet the challenge. HPD served as the Prime Consultant and developed an energy model for the chiller and boiler plant to develop energy reduction options models and establish Return on Investment (ROI). The ROI information was presented to Administration in order for them to make decisions on the energy features. The team agreed that there would not be any “bad” or “too complicated” ideas or strategies, only free thinking and open dialogue to determine the best possible solutions. We also agreed that any solutions to be considered would be substantiated by evidence and could not simply be a good idea. HPD and the TRMC team reviewed the existing plant’s components, configurations, operations, efficiencies and load profiles in order to identify opportunities for improvement. The review identified specific equipment that should be replaced, equipment that could be retrofitted and major controls upgrades needed to link the systems together. The team compiled a list of potential improvement items and tested each one in order to establish the potential savings, long term benefit, initial cost and estimated return on investment due to energy savings. The information was presented to senior leadership for review and discussion. The presentation allowed informed decisions to be made due to the research and proven data compiled by the team. Our efforts resulted in immediate approval of the recommended items and planned budgeting for the future projects.
The research, evidence and return on investment analysis resulted in:
-
Complete DDC controls upgrade for the chiller and boiler plant
-
Modifications to the existing piping arrangements to correct flow / distribution problems and prepare for the future change out of one chiller
-
New variable speed secondary pumps
-
New variable speed 900 - ton chiller with control modifications to the existing chillers
-
New Water side economizer
-
New 400 HP steam boiler with modulating burner and VFD blower controls
-
Upgrade to the two existing boilers to add modulating burner and VFD blower controls
-
New 1000 Kw generator to support one chiller on emergency power
-
New electronic generator monitoring and control system
The due diligence by the team on the front end and organized factual information presented to the decision makers resulted in funding for the projects, a reduction in operating cost, investment for the future needs and modernization of the plant.
Air Handling Unit Replacements and Upgrades
New Air Handling Units to replace units serving the Lab, Waiting and Radiology areas. Air Handling Unit and Chilled water conversion for the existing Medical Office Building. HPD designed a phased HVAC replacement to replace the existing Self Contained Water Cooled Unit system with a chilled water system.
ATRIUM NAVICENT HEALTH - MACON, GA
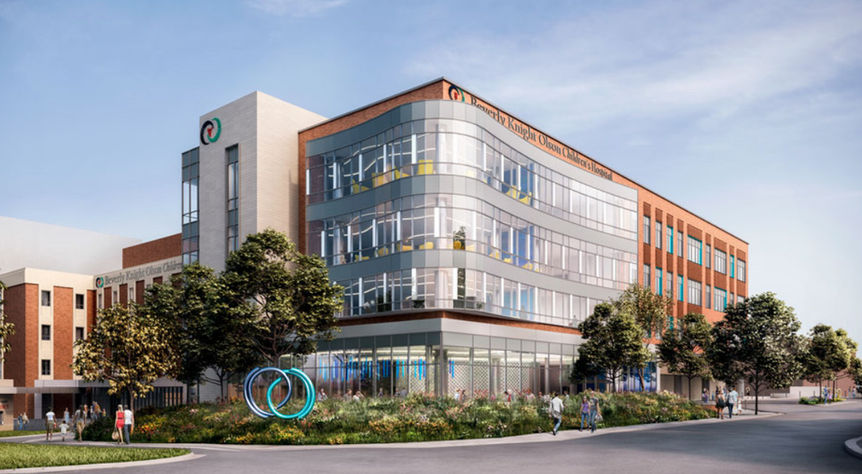
ATRIUM NAVICENT HEALTH - MACON, GA
HPD served as the Prime Consultant.
Chiller Plant Upgrade: Developed 3D model of the existing chiller plant to facilitate chiller, pump replacement and controls upgrades. Boiler Plant Upgrade/Replacement Steam and Hot Water: Downsized/replaced the existing steam boiler plant and added new dual fuel hot water boiler plant. Surgery Suite Sub Cooling HVAC Upgrade: Operating Suite Air Handling Unit replacement, OR interior Refresh and the addition of a Sub-Cooling Chiller system to provide 62 degrees at 40% RH conditions in the Operating Rooms.
CNN CENTER - ATLANTA, GA

CNN CENTER - ATLANTA, GA
HPD served as the Prime Consultant.
Generator and Critical Distribution Upgrade.
UPS Infrastructure Upgrade. Data Center Redundancy Upgrade. Air Handling Unit Upgrades.
REPLACEMENT HOSPITALS

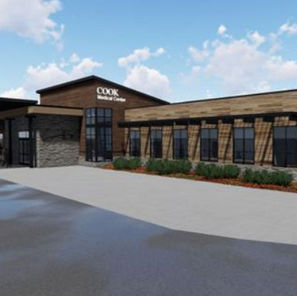

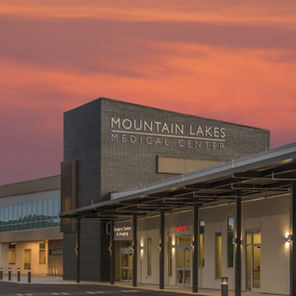
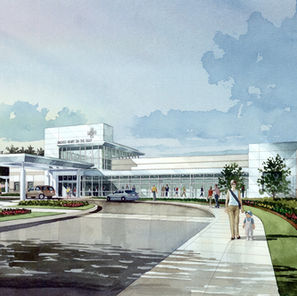
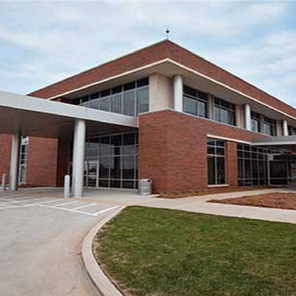

HOSPITALS CAMPUSES
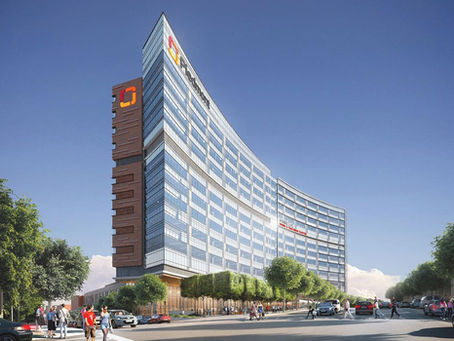
- Organ Recovery Center
- Women’s Center Renovation
- Emergency Department Expansion and Rehabilitation
- Rehabilitation Hospital
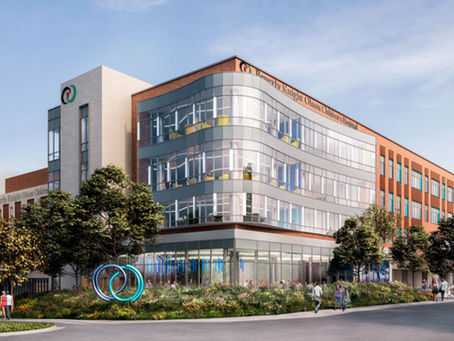
- Chiller Upgrade
- Boiler Plant Upgrade, Steam and Hot Water
- Operating Suite HVAC Sub-Cooling Upgrade
- Main Pharmacy Renovation

- Emergency Department and Operating Room Addition and Renovation
- Women’s Center

- Emergency Department Expansion
- Women’s Center
- Kitchen Renovation
- NICU Renovation
- Pharmacy
- Central Energy Plant Upgrade
- Heart Center - Cath Labs

- Cath Lab Addition and Renovation
- Emergency Department and Patient Tower Expansion
- Air Handling Unit Replacements and Upgrades
- Nuclear Camera Renovation
- Generator Plant Upgrade

- Women’s Pavilion
- Ambulatory Surgery Center
- Cath Lab Expansion
- North Patient Tower
- Emergency Department
- Open Heart Surgery Center
- Central Plant – Upgrade
- Medical Office Building
- Outpatient Surgery Center
- Parking Deck

- Free Standing Generator Facilities
- Surgery Suite HVAC Upgrade
- Bed Tower Addition and Renovations
- Labor and Delivery Expansion and Renovation
- Cancer Center Expansion and Renovations
- Pharmacy Renovation and Upgrade
- Outpatient Surgery Center
- Medical Office Building
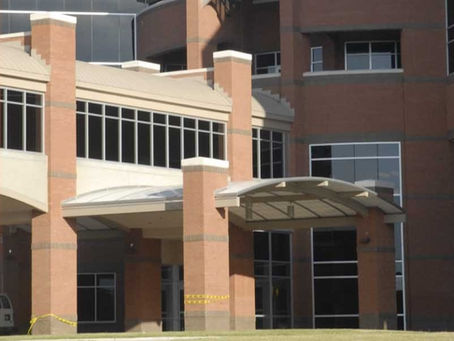
- Pharmacy Renovation
- Laboratory Upgrade Renovation
- MRI Replacement
- Emergency Department Renovation
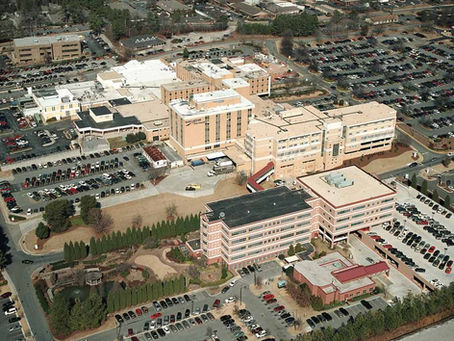
- Cancer Center Addition and Bridge
MEDICAL OFFICE BUILDING (MOB)

Five-story medical office building. An attached parking deck of 480,000 sq. ft. and future provisions for an additional 115,000 sq. ft. The project includes a 30,000 sq. ft. Ambulatory Surgery Center and a 12,000 sq. ft. Imaging Center.
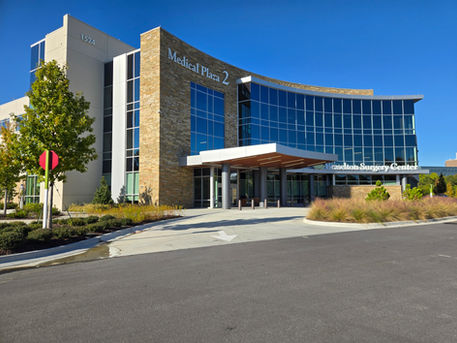
Three story, 90,000 sq. ft. medical office building. The first floor contains a 26,800 sq. ft. Ambulatory Surgery Center (ASC) with four OR’s, two procedure rooms, Prep/Post/PACU Rooms, Lab, Pharmacy, Sterile Processing, Sterile Storage, and support spaces. The upper two floors are shelled for future tenants.
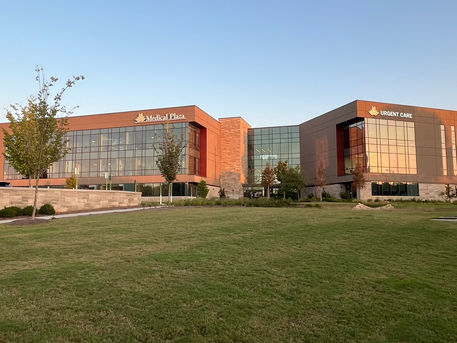
90,000 sq. ft. three story MOB that expands services into the Buford Area. Services include: Urgent Care, Physician Services, Cardiology, Imaging, and future Emergency Care.

Three story, 140,000 sq. ft. building with an open parking deck. The first floor holds a 33,000 sq. ft. Breast Center with MRI, CT, Ultrasound, Mammography, X-Ray, and Procedure suites. A 44,000 sq. ft. Pediatrics Center and 6,200 sq. ft. Administration area are located on the second floor. The third floor holds a 15,000 sq. ft. Internal Medicine suite, an 8,500 sq. ft. Doctor’s Office and a 19,700 sq. ft. Cancer Center with future provisions for a Nuclear Camera suite.

A 162,000 sq. ft. building offering Outpatient and physician services. 20,000 sq. ft. ambulatory surgery center includes 17 private, prep/recovery rooms, three operating room suites and three procedure rooms.

Four story 90,000 sq. ft. Medical Office Building. The lower level houses a 15,500 sq. ft. Imaging Center with MRI and CT suites. The first level provides 10,000 sq. ft. of Surgical Office space and 10,000 sq. ft. of Orthopedic Office space with two X-Ray rooms. The second level has a 3,000 sq. ft. Sleep Lab, a 10,000 sq. ft. Dermatology suite with two procedure rooms, a 3,000 sq. ft. Digestive Care suite, a 1,600 sq. ft. and Leg Care suite, and a 3,000 sq. ft. Oncology Center with seven infusion bays. The third level is comprised of a 3,600 sq. ft. Orthopedic Physical Therapy suite with a Procedure room, a 3,200 sq. ft. Vascular Surgery Office, and a 3,000 sq. ft. Urology suite.

Three story 80,000 sq.ft. building. The first floor offers 23,000 sq.ft. of orthopedic and spine care services. The second floor holds 23,000 sqft of Pain Management and Neurology Care suites. The third floor contains 22,000 sq.ft. of Physical, Occupational, Speech and Spine Therapy suites.
COMMUNITY
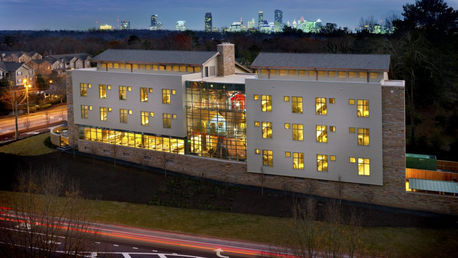
Three story facility which features guest rooms with private baths and roll in showers, a kitchen with a full pantry and dining areas, common family areas, a family kitchen, laundry facility, conference room and an arts and crafts activity room. The LEED Silver certified building utilizes a Variable Refrigerant System (VRF), Energy Recovery Unit, and Occupancy based lighting controls in all guest rooms to save energy.
NORTHSIDE GWINNETT ED EXPANSION

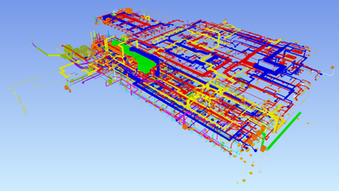
PIEDMONT ELLIJAY
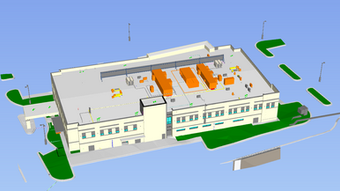
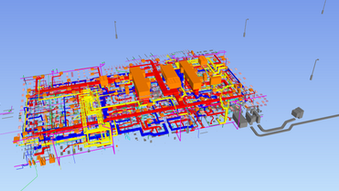

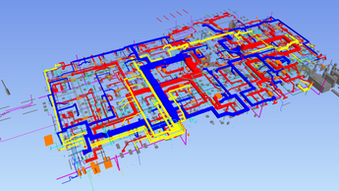
PIEDMONT NEWNAN EXPANSION


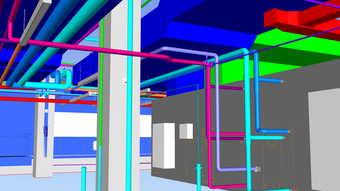
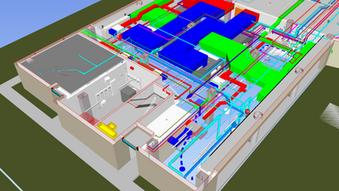
WARNER BROTHERS DISCOVERY CONTROL ROOM
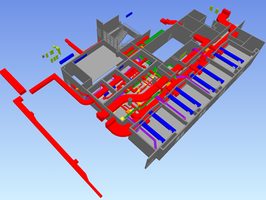


BROADCAST

A new speculatively designed building reconditioned to house Cable News Network, broadcast and administration activities. HPD, LLC provided HVAC, plumbing, fire protection and electrical engineering design services for this project. System design supported administrative areas, live broadcast areas, and production areas. The mechanical design included a dedicated chiller and chilled water system for technical areas; humidity control; acoustical treatment and cooling of electronic equipment racks.
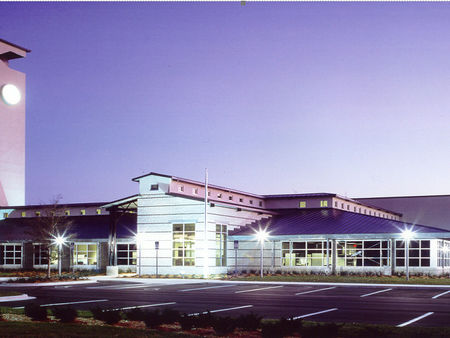
New television studio including: studios, editing suites, offices space, technical support space, and UPS/generator infrastructure.

Renovation and restack of an existing office building to include: Master Control Renovation, Graphic Renovation, and Espanol Studio.

New replacement facility for Georgia Public Television encompassing 230,000 sq. ft. of area and five levels. The Facility contains three production studios, five interactive/distant learning classrooms, control rooms, terminal gear, audio rooms, edit suites, music studio, talk studio and office support space. This facility is designed to be utilized by FEMA (Federal Emergency Management Agency) during times of natural disaster. Mechanical and electrical systems are designed for usage during prolonged power outages to support this facility. HPD was responsible for the design of all the HVAC, electrical and plumbing systems.

ATLANTA, GEORGIA
Multiple projects to support the development of the Turner Broadcast System Techwood Campus beginning in 1979. The complex includes: The Mansion, Market, Gate, Hub, Studios, and Overlook buildings. The campus includes: Media Operations, Administrative Offices, Studios, Editing Suites, Technical Support, Data Centers, and Restaurants. Central Plant utilities include: Chilled Water, Hot Water, UPS and Generator Infrastructure Support.
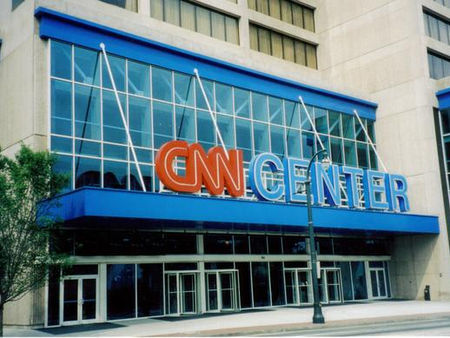
Multiple projects to support the development of the CNN Center Complex beginning in 1985. The complex includes: Headline News studios, editing suites, support office space, technical office space, photo lab, WCW wrestling studios, graphics, Spanish news network, Sports Illustrated network, terminal gear, data center, central plant upgrade, generator and UPS upgrades, and multiple master plans.
CORPORATE
SUMMITT PROPERTIES - Knoxville, Tennessee
Eighteen story office building with 450,000 square feet.
CRESCENT CENTER - Atlanta, Georgia
Twelve story office building with 300,000 square feet.
TRAVELERS INSURANCE OFFICE BUILDING - Atlanta, Georgia
Five story office building with 450,000 square feet.
NIGERIAN DIPLOMATIC MISSION BUILDING - New York, New York
Twenty-one story office building with 110,000 square feet.
TURNER BROADCASTING SYSTEMS OFFICE BUILDINGS - Atlanta, Georgia
Building A – Six Story 150,000 square feet
Building B – Five Story 190,000 square feet
Building C – Eight Story, 220,000 square feet
HEWLETT PACKARD REGIONAL OFFICE - Atlanta, Georgia
Five story corporate office building with 76,000 square feet.
HEWLETT PACKARD RESPONSE CENTER - Atlanta, Georgia
Two story data center with 90,000 square feet.
HEWLETT PACKARD BUILDING TWO - Kennesaw, Georgia
Single story data center with 105,000 square feet.
BELL SOUTH OFFICE BUILDING - Greenville, South Carolina
Three story corporate office building with 90,000 square feet.
PLAZA 400 OFFICE BUILDING - Atlanta, Georgia
Four story office building with 80,000 square feet.
PATEWOOD PLAZA - Greenville, South Carolina
Three story office building with 120,000 square feet.
TEXIZE OFFICE BUILDING - Greenville, South Carolina
Three story corporate office building with 120,000 square feet.
LIBERTY MUTUAL OFFICE BUILDING - Atlanta, Georgia
Three story corporate office building with 75,000 square feet.
HARTSFIELD COLONADE II - Atlanta, Georgia
Four story office building with 100,000 square feet.
GOVERNORS LAKE OFFICE BUILDING - Norcross, Georgia
1117 OFFICE BUILDING - Atlanta, Georgia
INDIAN RIDGE OFFICE BUILDING - Atlanta, Georgia
COBB MEDICAL OFFICE BUILDING - Austell, Georgia
ST. JOSEPH'S MEDICAL OFFICE BUILDING - Atlanta, Georgia
ST. JOSEPH MEDICAL OFFICE BUILDING - Augusta, Georgia
NORTHSIDE HOSPITAL MEDICAL OFFICE BUILDING - Alpharetta, Georgia
FLOYD MEDICAL OFFICE BUILDING - Rome, Georgia
BAPTIST NORTH MEDICAL OFFICE BUILDINGS I & II - Cumming, Georgia
CARTERSVILLE MEDICAL OFFICE BUILDING - Cartersville, Georgia
CEDAR LAKE MEDICAL OFFICE BUILDING - Biloxi, Mississippi
CEDAR LAKE SURGERY CENTER - Biloxi, Mississippi
CEDARTOWN MEDICAL OFFICE BUILDING - Cedartown, Georgia
COBB MEDICAL OFFICE BUILDING - Austell, Georgia
EASLAN MEDICAL OFFICE BUILDING - Spartenburg, South Carolina
EASTSIDE MEDICAL OFFICE BUILDING - Snellville, Georgia
FLOYD MEDICAL OFFICE BUILDING - Rome, Georgia
GEORGIA BONE AND JOINT MEDICAL OFFICE BUILDING - Cartersville, Georgia
HUTCHESON MEDICAL OFFICE BUILDING - Fort Oglethorpe, Georgia
KENNESTONE PHYSICIANS BUILDING - Marietta, Georgia
HENRY GENERAL MEDICAL OFFICE BUILDING - Stockbridge, Georgia
MEDICAL OFFICE BUILDING - Jefferson, Georgia
NORTHSIDE HOSPITAL MEDICAL OFFICE BUILDING - Alpharetta, Georgia
SHILLING MEDICAL OFFICE BUILDING - Lake City, Florida
ST. JOSEPH’S MEDICAL OFFICE BUILDING - Atlanta, Georgia
ST. JOSEPH’S MEDICAL OFFICE BUILDING - Augusta, Georgia
TIFT MEDICAL OFFICE BUILDING - Tifton, Georgia
MANUFACTURING

Two-story 35,000 square foot building to house: Office space, Fragrance R&D lab, Sample lab, Low odor threshold room, Perfumery and Evaluation offices, Temperature controlled storage area, Analytical GC/MS lab, Security Vestibule to meet the requirement of Homeland Security, Lobby/Art gallery and Smelling Booths with temperature and humidity control.

Contact Lens Manufacturing Plant including: Clean Rooms, Clean Storage, Packaging and Distribution and Office space.
CIBA VISION @ JOHNS CREEK - Duluth, Georgia
Research and Development Facility including Manufacturing, R&D Labs and Hazardous Product Containment and Support Spaces.
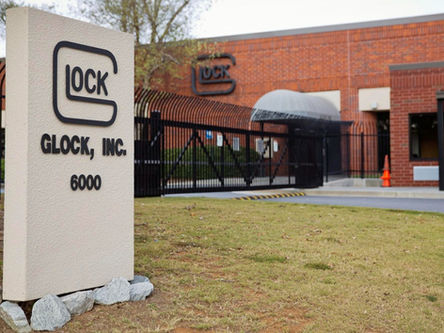
Glock is a fire arms manufacturer. The plant is a 70,000 square foot new facility connected to the existing facility. The facility includes a central energy plant (CEP) to house the required mechanical, electrical and fire protection systems. The design of the plant includes cooling and dehumidification of the plant, configured in a fashion that gives them maximum flexibility in locating equipment anywhere in the plant and the ability to relocate the equipment in the future. The CEP has provisions for expansion of the chilled water and Emergency power systems.